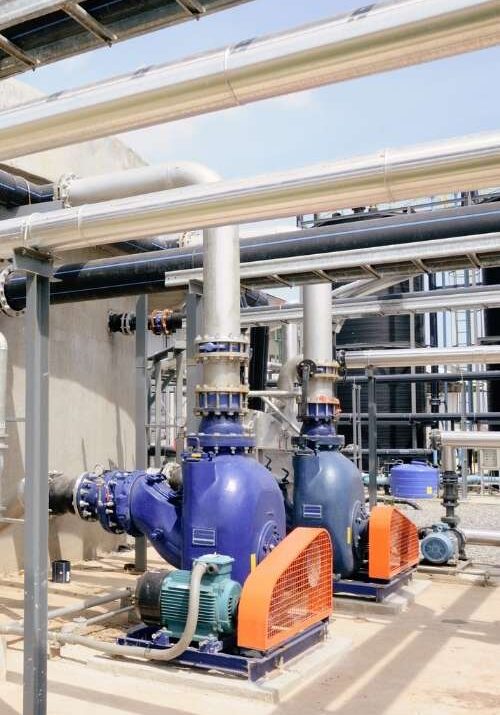
Bulk liquids pose an interesting challenge due to their typically high volume and the frequency of tanker loads. Facilities producing bulk liquids often have multiple tanker loads per week, and in some cases, even multiple loads per day. The management of these waste materials is crucial because if the bulk liquid waste cannot be hauled away, the tanks at the producer's facility will fill up, potentially leading to a shutdown of the entire operation. Therefore, it is essential for facilities creating bulk liquid waste to ensure a regular process of turning tanks to prevent disruptions to their operations.
Considerations in Handling and Recycling Bulk Liquids
One of the primary considerations in handling bulk liquids is the regularity of the process. Unlike solid waste or packaged waste that can sit in a corner without impacting operations, bulk liquids require ongoing handling to keep the plant up and running smoothly. Another challenge in handling liquid waste is related to tanker shipping. The number of liquid tankers available is generally low, and finding haulers who meet the necessary credentials and insurance requirements can be more difficult. Moreover, during colder months, liquid waste can solidify or freeze, causing offloading issues. There are also health and safety challenges associated with liquid waste, such as the risks involved in climbing on tanks or opening portals. These factors make the management of liquid waste a challenging task.
Additional Considerations when handling bulk liquids
Addressing Cold Weather Challenges
During the winter months in the Upper Midwest, innovative technologies and processes are employed to prevent freeze-up or solidification of certain bulk liquids that may come from meat processing facilities. Thawing processes or the use of heated tankers are employed to ensure a smooth flow of these liquids.
Loading Process and Access Control
Another critical aspect is the loading process, which requires careful consideration of the equipment used and the level of access drivers have to production facilities. Access to bulk liquid tanks at food plants is often controlled to ensure proper unloading. Collaboration with facilities that handle bulk liquids is essential to ensure the compatibility of the material with their systems.
Handling Different Types of Materials
Some materials have a slurry-like nature that may not flow through pump systems, while others may be highly viscous and require agitation and heating before being processed using sustainable or recycling technologies. Understanding the material properties and the requirements of the sustainable technology site is crucial for effective recycling.
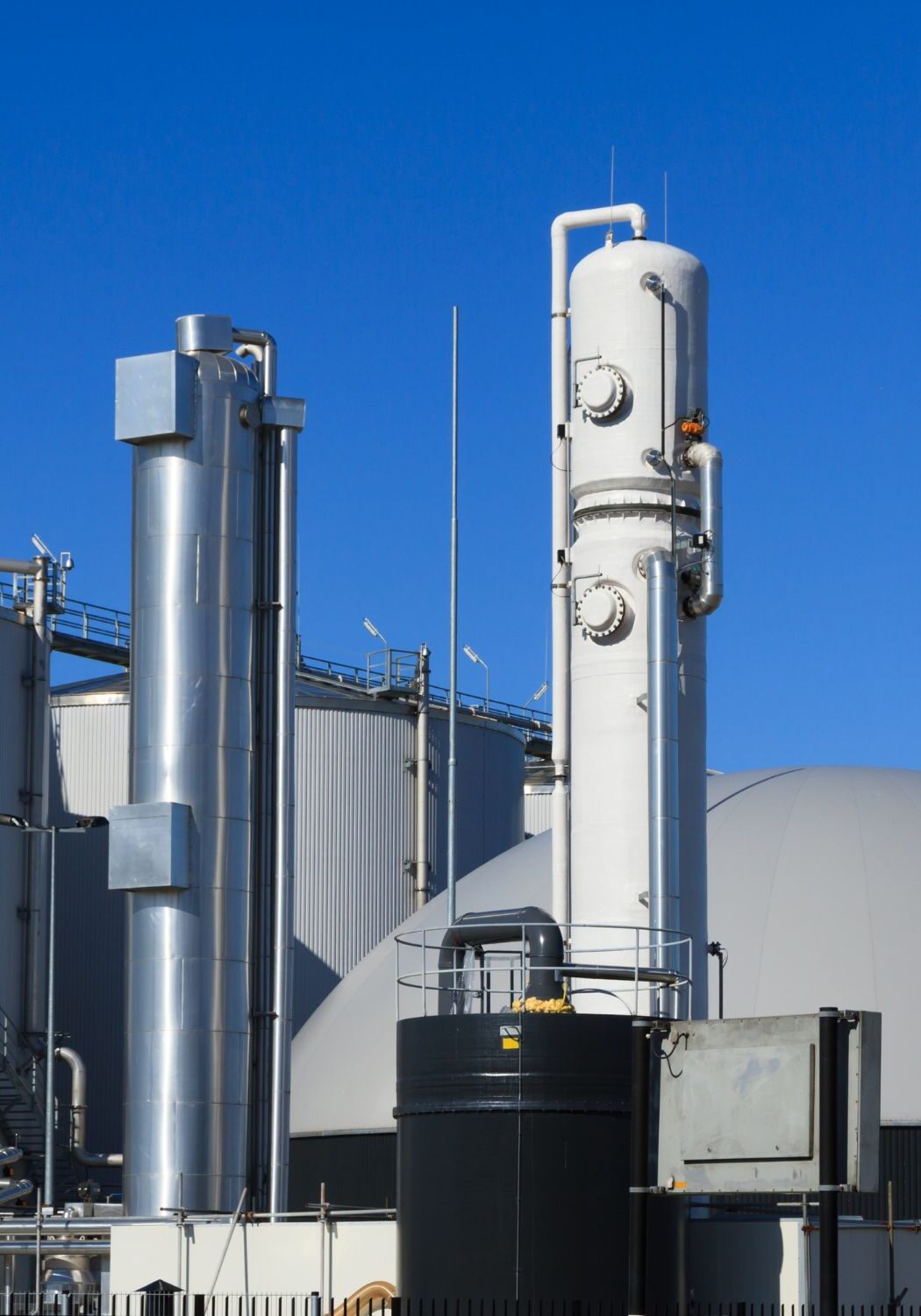